Silicone Keypad Customization: 5 Critical Considerations for Buyers
When designing a custom silicone keypad (silicone keypad), engineers and procurement teams must balance functionality, durability, and cost. Unlike standard keyboard components, custom silicone keypad solutions require meticulous planning across multiple technical and logistical factors.
Let's break down five essential considerations for successful customization.
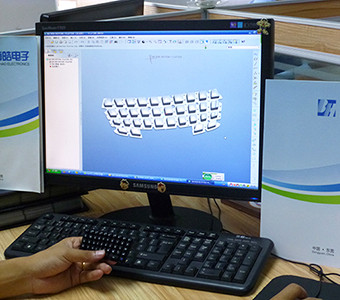
① Material Selection Matters
The foundation of any silicone keypad lies in its material. Opt for high-purity silicone rubber with certifications like FDA or RoHS for applications requiring food/medical safety. For industrial environments, flame-retardant grades (UL 94 V-0) are critical. Discuss environmental exposure (UV, chemicals, temperature ranges) with your keyboard custom supplier to avoid premature degradation.
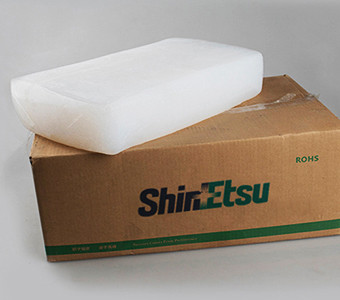
② Design Complexity Impacts Costs
A silicone keypad’s tactile performance stems from its dome structure and thickness.
However, over-engineered features like multi-layer backlighting or hybrid metal-silicone assemblies can inflate tooling fees by 30–50%.
Use CAD simulations to validate button travel force (typically 180–350gf) and lifespan before finalizing mold designs with your silicone keypad manufacture partner.
③ Supplier Expertise Dictates Quality
Verify if your keyboard custom supplier has in-house tooling capabilities. Suppliers outsourcing mold-making often lack quality control.
Ask for ISO 9001 certification and request samples from previous projects.
For RGB backlit keypads, confirm their experience with light-guide film integration to prevent uneven illumination.
④ Prototyping & Testing Cannot Be Rushed
Avoid skipping Design for Manufacturability (DFM) reviews. A pre-production prototype phase allows adjustments to embossing depth (critical for braille keypads) or carbon pill alignment.
Conduct environmental tests: 100,000+ press cycles for consumer electronics, IP67 sealing validation for outdoor devices.
⑤ Volume Scalability Determines ROI
Low-volume orders (<5,000 units) often use soft tooling, cutting initial costs but sacrificing consistency. For high-volume production (>50k units), invest in hardened steel molds. Negotiate tiered pricing with your silicone keypad manufacture partner and clarify post-sale support terms for mold storage/repairs.
A successful custom silicone keypad project requires synergy between technical specifications and supply chain pragmatism. By prioritizing certified materials, DFM reviews, and transparent supplier partnerships, brands can achieve tactile precision and long-term reliability. Partner with experienced silicone keypad manufacture experts to navigate these critical steps.
Feel free to contact fromrubber. Custom experts are on hand to provide professional advice.
Customize page:https://www.fromrubber.com/
Contact information:https://www.fromrubber.com/contact-us.htm