Home / All / Silicone Rubber Keypad / Meter Instrument Keypad /
Custom Silicone Rubber Conductive Keypad For Pos Machine | Good Tactile Feedback
Custom Silicone Rubber Conductive Keypad For Pos Machine | Good Tactile Feedback
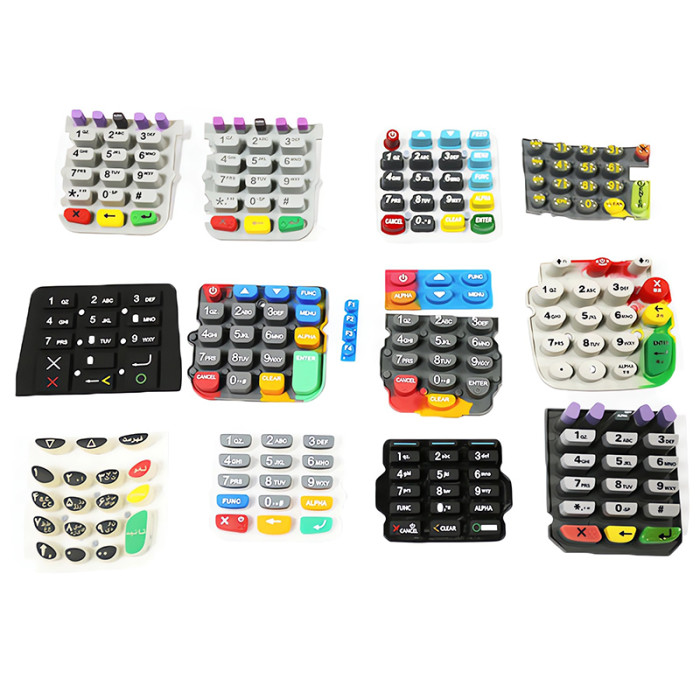
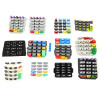
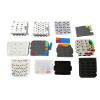
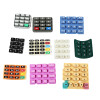
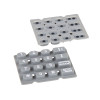
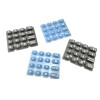
Categories | Meter Instrument Keypad |
---|---|
Brand | FromRubber Silicone & Plastic OEM Manufacturer |
Design | Follow 3D Drawing Or Physical Object |
Printing | Silk Screen Printing |
Conduction Mode | Conductive Carbon Pills |
MOQ | 1000pcs |
Application | Pos Machine |
Terms of Payment | L/C, D/A, D/P, Western Union |
Update Time | Jan 22,2025 |
Detail Information
Manufacture And Design Silicone Rubber Pos Machine Keypad
Manufacturing silicone keypads for POS machines involves several steps to ensure durability, functionality, and compliance with the machine's specifications. Here's a step-by-step guide to help you understand the process:
1.Design and Mold Creation
Sketch the layout: Define the key positions, shapes, sizes, and any special features like backlighting or symbols.Software Design: Use CAD software to create a detailed design.
Mold Design & Fabrication: Based on the CAD design, create a mold, usually from metal. The mold design is critical for the shape and quality of the final product.
2. Material Selection
Choose the appropriate type of silicone:Liquid Silicone Rubber (LSR): Known for its strength, flexibility, and ability to mold intricate designs.
High Consistency Rubber (HCR): Used for more robust applications.
3. Silicone Preparation & Coloring
Mixing: Mix the base silicone with curing agents and other additives as required.Coloring: Add color pigments as per the keypad design specifications.
4. Molding Process
LSR Injection: The liquid silicone rubber is injected into the molds under high pressure.Curing/Heating: The silicone is cured by heating inside the mold, usually between 120-150°C.
HCR Compression: Place pre-measured silicone rubber into the mold cavity and compress it.
Heating to Cure: Similar to injection molding, the silicone is then cured with heat.
5. Post-Molding Processes
Surface Treatment:Coating: Apply coatings for improved abrasion resistance or tactile feel.
Laser Etching: Laser etch the symbols and characters on the keys for clear visibility.
Printing and Finishing:
Screen Printing: Print any additional symbols or colors needed.
Protective Coatings: Apply protective layers to enhance durability and appearance.
Trimming:
Remove excess material (flash) from the keypads using mechanical or manual trimming.
6. Quality Control
Inspection: Check dimensions, tactile response, color consistency, and other specifications.Functionality Testing: Ensure keys operate correctly and respond well to user interaction.
7. Assembly
Fit the silicone keypads into the POS machine housing.Electrical Contacts: Ensure that the keypads provide proper tactile feedback and electrical signaling.
Packing: Pack the finished keypads according to industry standards to prevent damage.
Shipping: Arrange for distribution and delivery to POS machine manufacturers.
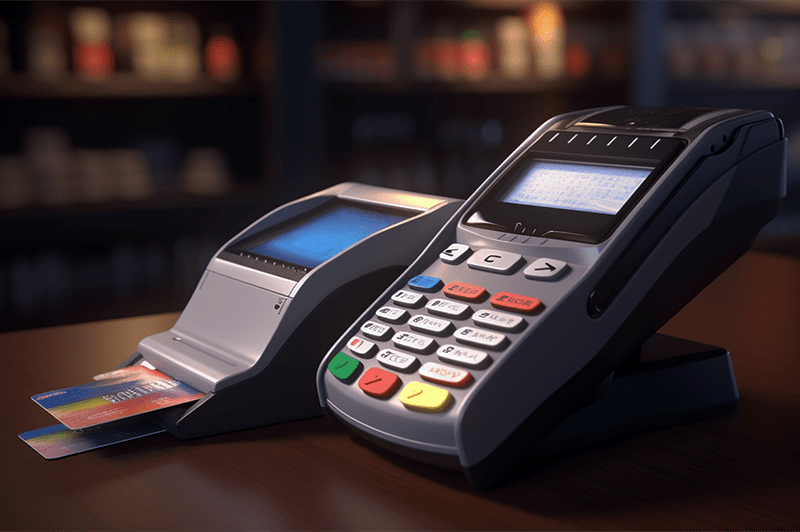
For pos machine manufacturer
provide free design consultation for upgrading
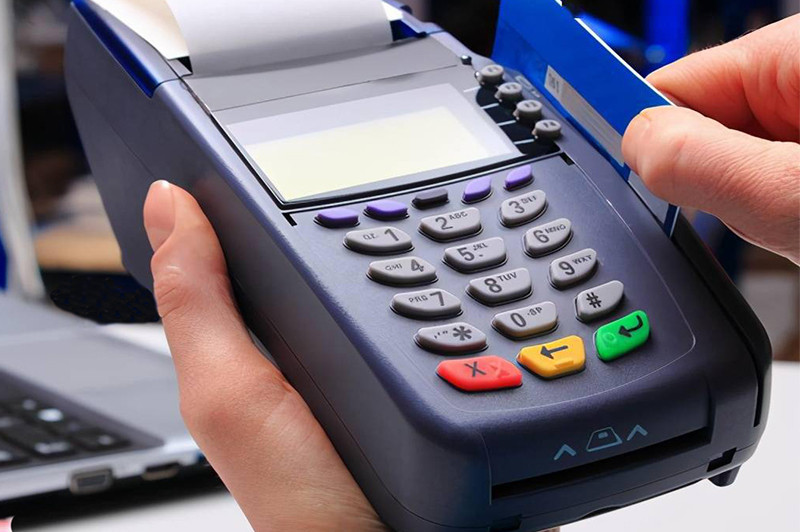
For pos machine parts wholesaler
Provide POS machine silicone keypad production
Understanding Snap Ratio in Rubber Keypads and Its Impact on Tactile Feedback
The snap ratio in rubber keypads refers to the relationship between the actuation force and the tactile force during the button-press action. Essentially, it determines how responsive and satisfying the button press feels to the user.
Here’s how it works:
Optimal Range: Ideally, a snap ratio between 40% and 60% provides a balanced experience. This range offers a good combination of a responsive snap action and a longer lifespan for the keypad.
Lower Snap Ratios: If the snap ratio drops below 40%, the tactile feedback diminishes. Users might notice that the button press feels less distinct, although this setting can actually prolong the switch's life.
Higher Snap Ratios: Conversely, snap ratios above 60% might improve the tactile feedback, making the button feel more immediate and crisp. However, this could potentially reduce the keypad’s durability over time.
Key Takeaways
Snap Ratio Definition: The relationship between the immediate response (snap action) and the force applied.
Optimal Snap Ratio: 40% to 60% for a balance of feel and durability.
Impact of Lower Ratios: Less tactile feedback but extended switch life.
Impact of Higher Ratios: Better tactile feedback but potentially shorter lifespan.
Understanding these dynamics helps in designing keypads that meet both user satisfaction and durability expectations.
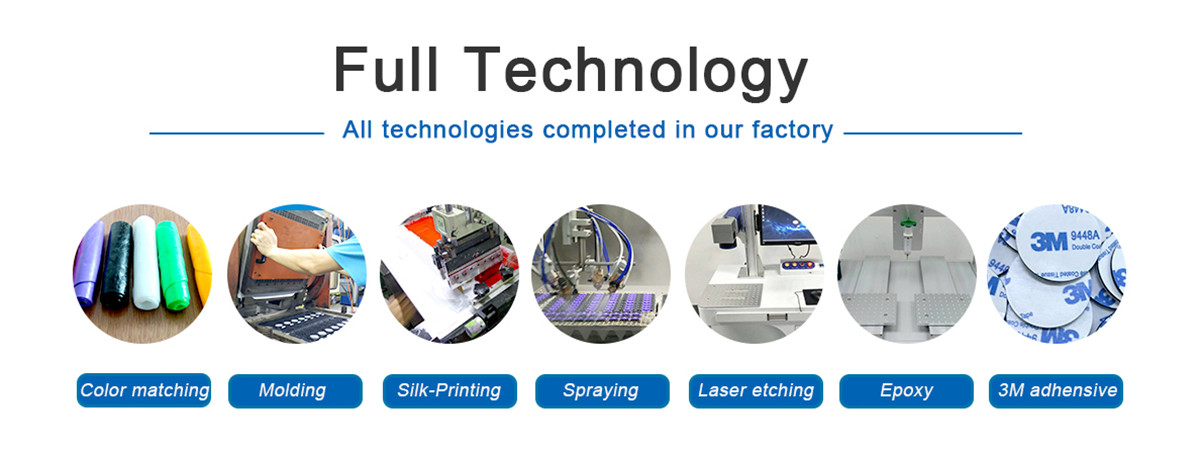
Review
- Loading...
Related Products
Start Your Project Today!
-We are not just a manufacturer of silicone/plastic products, we focus on your business and help you achieve your long-term goals.
- Tel
- *Title
- *Content